Slimline Range / General Purpose
General purpose thermal and environmental chambers
Typical Applications
- Process drying where temperature uniformity is essential, e.g., pharmaceuticals
- Stabilising products prior to installation or more demanding testing
- Temperature/humidity testing under fixed or cyclic conditions, satisfying numerous IEC 60068 test requirements plus a wide range of equivalent specifications
Advantages
Small Footprint & Easy to Move
Designed to have a small footprint while maintaining excellent performance, eg the Slimline 450 model has a 0.7m2 footprint. Large, lockable castors make moving the chambers very easy.
Good Circular Airflow
Air is drawn in to the centre of the rear wall, conditioned in the plenum before re-entering the chamber at the front through a grill by the door.
Ideal for General Purpose Testing
The Slimline range was designed to suit general purpose applications, such as small electronic modules, sub-assembly testing, etc. where good control at specific conditions is required.
Wide Temperature and Humidity Ranges
Temperature ranges of +180°C to either -40°C or -70°C are available and the Slimline range is renowned for is wide humidity conditions which exceed Area ‘A’ – the norm for most chambers in this category.
Capacitive Humidity Probe
All Slimline humidity chambers are fitted with a high-quality, no-maintenance capacitive humidity probe, for hassle free humidity testing.
Suitable for a large range of Test Standards
Slimline chambers are used by a wide range of industries, from Oil & Gas to Aerospace and Pharmaceutical, to achieve their specific Test Standards, as well as International Standards such as IEC60068 (Environmental Testing of Electrotechnical Products).
Suitable for a large range of Test Standards
Slimline chambers are used by a wide range of industries, from Oil & Gas to Aerospace and Pharmaceutical, to achieve their specific Test Standards, as well as International Standards such as IEC60068 (Environmental Testing of Electrotechnical Products).
Custom versions available
As well as the standard range of Slimline chambers, our inhouse design and manufacturing in the UK, means we have produced many custom versions of the Slimline range including Fast Shock (Oil & Gas), Humidity Drying (Pharmaceutical) and many more…
SIMPLEtouch
Touch Screen Programmer
Easy set-up and monitoring of chamber conditions, simplifies programming of complex cycles… read more
Benefit | Achieved by |
---|---|
High performance | Uniform temperature throughout the interior (indicated by low thermal gradients) – air drawn in at the centre of the rear wall is conditioned in the plenum before re-entering the chamber through a grill near the door |
PT100 sensor for stable and reliable temperature measurement | |
Capacitive humidity sensor gives optimum combination of accuracy, rapid response and reliability | |
Chambers built from high quality components ensuring long service lifetimes | |
Flexibility | Wide range of volumes – 27 to 1000 litres – within a compact chamber design |
Labview-based user interface developed by Sharetree and easy to upgrade and customise | |
Modbus communications over a range of different interfaces | |
Extensive list of options and customisations | |
Easy to use and maintain | Factory-calibrated and simple to install |
Uses readily available components | |
Operates from single-phase mains power supply | |
PC-based touchscreen control panel – connects to industry standard PID controller that is readily maintained or replaced, minimising downtime |
Temperature Uniformity and Stability Specifications* (all models) | ||
---|---|---|
Thermal Gradient (<100°C) | ± 2 | °C |
Thermal Gradient (>100°C) | ± 2 | % of temperature |
Temperature Fluctuation | ± 0.3 | °C |
*Measured after stabilisation (IEC 60068-3-5) |
Slimline Thermal Chambers
Choose from three different cooling mechanisms depending on your requirements.
Compressor Cooling
- Refrigerant gases in a closed-loop system are repeatedly compressed and expanded to cool the air in the chamber (same principle as domestic refrigerators)
- Maximum temperature = +180°C; minimum temperature = -40°C (single-stage compression) or -70°C (multi-stage or cascade compression)
- Temperature ramp rate = 1-2°C/min (standard); high-performance models achieve better than 3°C/min
- Offers reliable continuous operation with no ancillary services required
- Ideal for testing electronic assemblies with low heat dissipation
Internal Size (mm) | Type | External Size (mm) | Temp Range | ||||||
---|---|---|---|---|---|---|---|---|---|
Model | W | D | H | Ltrs | W | D | H | Max | Min |
TC Slimline 300 -40 ME | 300 | 300 | 300 | 27 | 575 | 785 | 1025 | 180 | -40 |
TC Slimline 450 -40 ME | 450 | 450 | 450 | 90 | 725 | 935 | 1225 | 180 | -40 |
TC Slimline 450 -70 ME | 450 | 450 | 450 | 90 | 725 | 935 | 1225 | 180 | -40 |
TC Slimline 600 800 -40 ME | 600 | 800 | 600 | 288 | 875 | 1285 | 1330 | 180 | -40 |
TC Slimline 600 800 -70 ME | 600 | 800 | 600 | 288 | 875 | 1285 | 1330 | 180 | -70 |
TC Slimline 750 800 -40 ME | 750 | 800 | 750 | 450 | 970 | 1320 | 1650 | 180 | -40 |
TC Slimline 750 800 -40 ME | 750 | 800 | 750 | 450 | 970 | 1320 | 1650 | 180 | -70 |
TC Slimline 600 1000 -40 ME | 600 | 1080 | 1000 | 650 | 820 | 1570 | 2130 | 180 | -40 |
TC Slimline 600 1000 -70 ME | 600 | 1080 | 1000 | 650 | 820 | 1570 | 2130 | 180 | -70 |
TC Slimline 1000 -40 ME | 1000 | 1000 | 1000 | 1000 | 1220 | 1570 | 2130 | 180 | -40 |
TC Slimline 1000 -70 ME | 1000 | 1000 | 1000 | 1000 | 1220 | 1570 | 2130 | 180 | -70 |
Indirect Liquid Nitrogen (LN2) Cooling
- Liquid nitrogen used as a refrigerant to indirectly cool the air in the chamber (nitrogen gas is then vented to atmosphere)
- Safer than direct LN2 injection – normal levels of oxygen are always maintained inside the chamber
- Maximum temperature = +250°C (standard models +200°C); minimum temperature = -70°C
- Temperature ramp rate = 10°C/min
- Requires continuous supply of LN2 and safe venting of nitrogen gas during operation
- Can cope with greater heat output from components under test than compressor cooling
Ideal for thermal stressing and accelerated life testing
Internal Size (mm) | Type | External Size (mm) | Temp Range | ||||||
---|---|---|---|---|---|---|---|---|---|
Model | W | D | H | Ltrs | W | D | H | Max | Min |
TC Slimline 300 -40 LN | 300 | 300 | 300 | 27 | 575 | 785 | 1025 | 250 | -70 |
TC Slimline 450 -40 LN | 450 | 450 | 450 | 90 | 725 | 935 | 1225 | 250 | -70 |
TC Slimline 450 -70 LN | 450 | 450 | 450 | 90 | 725 | 935 | 1225 | 250 | -70 |
TC Slimline 600 800 -40 LN | 600 | 800 | 600 | 288 | 875 | 1285 | 1330 | 250 | -70 |
TC Slimline 600 800 -70 LN | 600 | 800 | 600 | 288 | 875 | 1285 | 1330 | 250 | -70 |
TC Slimline 750 800 -40 LN | 750 | 800 | 750 | 450 | 970 | 1320 | 1650 | 250 | -70 |
TC Slimline 750 800 -40 LN | 750 | 800 | 750 | 450 | 970 | 1320 | 1650 | 250 | -70 |
TC Slimline 600 1000 -40 LN | 600 | 1080 | 1000 | 650 | 820 | 1570 | 2130 | 250 | -70 |
TC Slimline 600 1000 -70 LN | 600 | 1080 | 1000 | 650 | 820 | 1570 | 2130 | 250 | -70 |
TC Slimline 1000 -40 LN | 1000 | 1000 | 1000 | 1000 | 1220 | 1570 | 2130 | 250 | --70 |
TC Slimline 1000 -70 LN | 1000 | 1000 | 1000 | 1000 | 1220 | 1570 | 2130 | 250 | -70 |
Forced Ambient Air Cooling
- Range of heat-only chambers (ovens) with same dimensions and volumes as ranges above (model numbering TC Slimline 300 FAC, etc)
- Controlled cooling to avoid thermal shocking of components under test
- Maximum temperature = +250°C; minimum temperature = ambient + 20°C
Slimline Environmental Chambers
Combine temperature cycling with precise control of the relative humidity.
- Same cooling mechanism as compressor-cooled thermal chambers
- Maximum temperature = +180°C; minimum temperatures = -40°C (single-stage compression) or -70°C (multi-stage or cascade compression)
- Water vapour added to air from heated water bath and removed through condensation on cooled copper coil
- Relative humidity = 10-96% over temperature range of 10-100°C (Area ‘A’ in chart)
Humidity – Standard Operating Regions
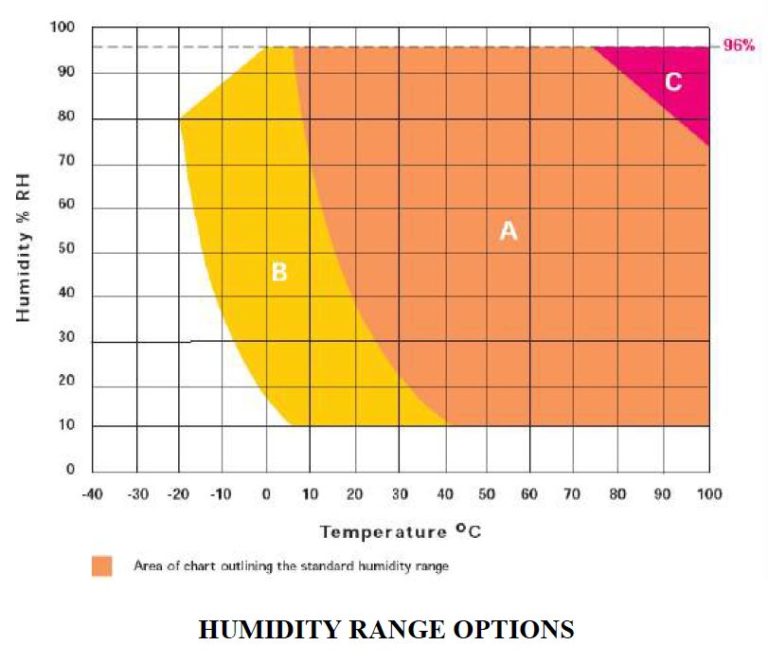
A – Typical region of humidity control in chambers
B / C – Optional regions for specialised applications
Internal Size (mm) | Type | External Size (mm) | Temp Range | Humidity Range | ||||||
---|---|---|---|---|---|---|---|---|---|---|
Model | W | D | H | Ltrs | W | D | H | Max | Min | %RH |
TC Slimline 450 -40 ME | 450 | 450 | 450 | 90 | 725 | 935 | 1225 | 180 | -40 | Area 'A' |
TC Slimline 600 800 -40 ME | 600 | 800 | 600 | 288 | 875 | 1285 | 1330 | 180 | -40 | Area 'A' |
TC Slimline 600 800 -70 ME | 600 | 800 | 600 | 288 | 875 | 1285 | 1330 | 180 | -70 | Area 'A' |
TC Slimline 750 800 -40 ME | 750 | 800 | 750 | 450 | 970 | 1320 | 1650 | 180 | -40 | Area 'A' |
TC Slimline 750 800 -40 ME | 750 | 800 | 750 | 450 | 970 | 1320 | 1650 | 180 | -70 | Area 'A' |
TC Slimline 600 1000 -40 ME | 600 | 1080 | 1000 | 650 | 820 | 1570 | 2130 | 180 | -40 | Area 'A' |
TC Slimline 600 1000 -70 ME | 600 | 1080 | 1000 | 650 | 820 | 1570 | 2130 | 180 | -70 | Area 'A' |
TC Slimline 1000 -40 ME | 1000 | 1000 | 1000 | 1000 | 1220 | 1570 | 2130 | 180 | -40 | Area 'A' |
TC Slimline 1000 -70 ME | 1000 | 1000 | 1000 | 1000 | 1220 | 1570 | 2130 | 180 | -70 | Area 'A' |
Options and Customisation
Call Sharetree on 01453 828 642 for your specialist requirements.